An Introduction To Mechanical Pins And Their Uses
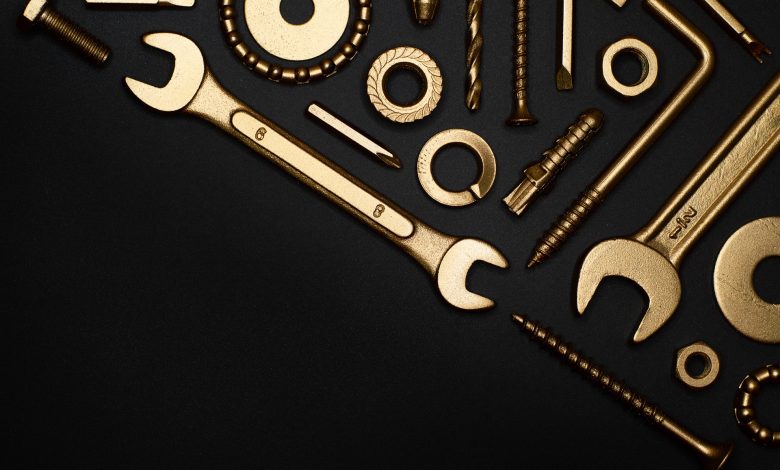
Mechanical pins are useful for securing shaft-supported parts to the shaft, preventing axial movement caused by thrust stress while also allowing torque transmission.
Machine pins, also known as pin fasteners or fastening pins, are a type of specialty fastener used to align and attach two pieces or components properly. The Straight pin, which has a circular cross-section by its diameter and length, is the most basic sort of pin.
Installation and removal of these fasteners, which are available in semi-permanent and rapid types, may require additional pressure or tools, or they may include a spring-loaded mechanism that locks them into place for ease of installation and withdrawal.
You can use pins in a variety of ways to secure the shaft to its surroundings. Pins aren’t just for attaching shafts to other components; they’re also useful for a variety of other things.
In this article, we will discuss different types of mechanical pins and their uses in detail.
Importance of mechanical pins
Fasteners are typically the smallest and least expensive parts in a machine but manufacturers rely on them to keep whole assemblies together for years or decades. Bolts, rivets, bolts, and pins, to mention a few, can be useful to hold components together.
There are two types of assembly techniques: ways that require two components or two operating procedures to hold pieces in place, and methods where the parts are self-retaining. The design engineer’s task is to select a solution that gives the highest quality joint with long-term integrity at the lowest production cost.
Types of pins
Mechanical pins made of steel are better for all applications where two pieces require a precise union. They can secure two things together as a hole alignment assist.
Mechanical pins come in a variety of shapes and sizes, with the following being the most common:
- Drive pins
- Groove pins
- Spiral groove pins
- Threaded taper pins
- Roller pins
- Circle cotters
- Clinch pins
- Extended cotter pins
- hairpin clips
- Ring cotter pins
- Cotter pins
- Hitch pins
- Bullet-nose pins
Drive pins
Drive pins must fit into position since they have an interference fit. They’re frequently utilized to put together components in rotational or other moving machines.
Groove pins
Pins having longitudinal grooves are groove pins. They’re meant to link two parts together. Grooves increase the adhesive’s surface area and thus its gripping strength.
Spiral groove pins
Cylindrical pins with parallel grooves are spiral groove pins. They’re employed to link two parts together. Grooves increase the adhesive’s surface area and thus its gripping strength.
Threaded taper pins
Threaded taper pins have the same size as ordinary taper pins, with the exception that they feature a threaded part on the smaller end. When removal is necessary, threaded taper pins are essential.
Roller pins
Rolled steel or other material rolls into a cylindrical shape to make roll pins or slotted steel springs. The slot in these headless, hollow pins runs longitudinally running the length of the pin.
Circle cotters
Circle cutters are typical of wire that has been wrapped or turned on from the center outward. The cotter’s open end is threaded into a pin’s hole, then rotated until it snaps into place.
Cotters in a circle are quite secure. They’re employed in situations where sharp edges aren’t allowed, such as fabric applications.
Clinch pins
Cotter pins are a type of clinch pin. They have a hump on one end when they’re made. Clinch pins are self-securing and do not need the ends of the pins to bend.
Extended cotter pin
Split pins that open outward after going through a hole are cotter pins. The extended cotter pin is the most common, with one end that is somewhat longer than the other. Cotter pins are frequently used in tandem with clevis pins. Split pins are another name for cotter pins.
Hairpin clips
External hitch pin clips are reusable pins that are also called hairpin clips. One-half of the hairpin clip has an uneven bulb and wave. The pin’s opposite half is straight.
The assembly of components is held tight by the elastic deformation of this type of pin, which creates a cavity between the wavy and straightened ends. These are necessary to immediately put together or take apart components.
Ring cotter pins
Ring cotter pins are a cross between a circle cotter and a twist pin. One side of the wire clip is kept flat, while the other helices around and under the straightened side before being sent across the straight side. When components are fixed properly, this helix and twist approach offers an automatic, secure lock.
Cotter pins
Cotter pins are held in place by clevis pins. On one end, they have ahead, and on the other, they have a hole. The cotter pin fits into the hole. Clevis pins are removable connectors that connect two components.
Hitch pins
Hitch pins connect or “hitch” two components temporarily. They are useful with a cotter pin or a safety pin that’s built-in. Hitch pins are usually with a wire loop grip on one end to make them easier to remove.
Bullet-nose pins
To align two parts of a fixture, bullet-nose pins are essential. The tip is either short, spherical, or diamond. Bullet-nose pins require a matching bushing or liner to provide a precise fit with the pin nose.
Round and diamond bullet-nose pins are frequently in use in combination. The round pin is the main, 2-axis locator in these circumstances, whereas the diamond pin is the secondary, 1-axis finder.
Conclusion
To conclude, in addition to the features listed above, these components come in several sizes and materials, including metal, plastic, and wood, as well as varied designs to fit a wide range of applications.
Since each type of pin conducts different roles and processes, determining the best type of machine pin to use is highly dependent on the application’s requirements.
Design engineers rarely receive formal instruction in the mechanics of attaching and joining, despite the importance of pins. Pins are not in the notice until the very end of the design process.
Perhaps, make sure you choose verified and authentic makers of these pins. Such as pin shaft manufacturers you select for your assembly line or the quality of pins for your machines.